导读:药物对人类健康以及日益增长和老龄化的全球人口的福祉至关重要。然而,批量合成方法在工艺生产率方面存在局限性,导致反应混合物的混合效率低下,热量和物质传递特性有限,以及较低的工艺安全度。
药物活性成分的生产被认为是化学行业中最耗能和耗材的行业之一,仅在2023年就贡献了358百万吨的温室气体排放。这相当于全球二氧化碳排放的6%,超过了汽车行业的排放。
药物在批量和流动两种方式下均已工业化生产。通过比较,作者提供了批量和连续流动技术的综合分析,包括技术经济和生命周期评估。随小编一起看看,一起来看看这些令人瞩目的创新成果吧!
批量和连续流动技术综合分析

1、溶剂用量减少
连续流动系统通常在较低的温度和压力下运行,从而更有效地利用试剂和溶剂。这种效率导致冷却和清洁单元操作所需的水使用量减少。
此外,连续流动系统的紧凑设计和对反应参数的增强控制进一步减少了对溶剂和水的需求。因为反应在更受控和稳态的环境中进行,最小化了在处理和加工阶段对多余水的需求。
较低的水使用量可以与减少的电力消耗相关联,因为所需的能量更少用于冷却和处理操作的要求。因此,这一线性关系体现在其对整体能源消耗和环境可持续性的潜在影响上,是评估制造过程中的一个关键考虑因素。
土地系统变化的影响考虑了技术对森林砍伐和自然栖息地破坏的影响。流动设备占地面积小,与批量生产相比,具有明显的优势。
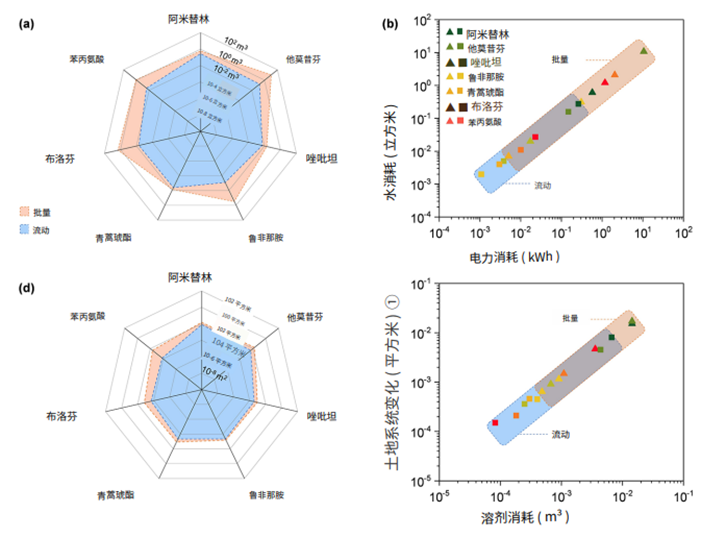
图1.土地系统变化与溶剂使用之间的相关性
在布洛芬生产过程中,获得的最大减少为99%,每克目标产品的总溶剂使用量从批量过程中的20.70m3减少到连续流动法中的5.4m3。土地系统变化,苯丙氨酸工艺表现最佳,批量法的每克产品0.00468m2减少到流动法的0.00015m2 ,减少了97%。
2、能耗断崖式下降在连续流动系统中观察到的能源效率提高归因于连续流动技术固有的几个特性。能源效率主要与过程持续时间相关。这表明,在连续流动系统中,较短的反应时间固有地需要更少的电力,从而推动了总能源消耗的减少。

图2.七个批量和流动过程的总能源消耗与过程持续时间之间的相关性
布洛芬作为全球用量最大的非甾体抗炎药,传统批处理工艺存在反应时间长、溶剂消耗大、能耗高等问题。通过优化为连续流工艺,能耗降低97%,实现了成本与效率的双赢,不仅显著减少了环境影响,还提升了生产经济性。
3、降低碳排放药物制造过程,特别是在其对温室气体排放的有显著贡献。碳排放可能来自多种来源,包括加热、冷却或相变所需的能量密集型热过程,以及溶剂蒸发、试剂分解和副产物形成。
此外,排放可能还源于上游活动,如原材料提取、运输和净化,以及下游处理步骤,如分离、纯化和废物处理。因此,作者还对批量和流动方法的碳(CO2)排放进行了评估。

图3.对批量和流动方法的碳(CO2) 排放评估
流动技术显著降低了碳排放,平均减少了79%,减少了一个数量级。布洛芬工艺表现出减排性能,从排放0.41kgCO2equiv降至0.01kgCO2equiv,减少了97%。苯丙氨酸工艺也遵循了这一良好趋势,二氧化碳排放从0.43kgCO2 equiv减少了95%,降至0.02kgCO2 equiv。
4、投资和运营成本
在从批量方法转向连续流动方法的过程中,由于反应器尺寸较小,资本成本可能会降低。这种降低对于制药行业尤其有利,因为高额的初始投资可能会阻碍新技术的采用。
例如,对于高产量的成熟产品,企业可能会发现采用流动制造具优势,在这种情况下,资本节省可以随着时间的推移与运营效率相辅相成,或者在推出新药品时进行新产品开发。这种方法使公司能够设计专门优化为连续流动的工艺,避免了改造现有批量系统所带来的复杂性和成本,从一开始就促进了先进技术的顺利整合。

图4七个批量和流动过程的资本成本支出,批量转流动的成本降低(a),资本成本结果的统计分析(b),七个批量和流动过程的年运营成本(c),运营成本结果的统计分析(d)
批量配置的估计成本在$3,000,000到$7,000,000之间,而连续流动技术的成本范围为$2,000,000到$4,000,000。从经济角度来看,连续流动法对资本成本支出有一定幅度的下降。
在鲁非那胺工艺中观察到的资本成本降低表现最佳,几乎下降了50%,从$7,030,000降至$3,520,000。然而,资本成本的降低是依赖于具体案例的。05E因子通过评估七个过程的绿色性,考虑E因子(每单位产品的废物质量)对其环境表现进行了调查。图5.批量和流体化学中七个工序的E因子相对于目标产品,连续流动过程产生的过程较少。事实上,批量工艺的E因子范围在10到110之间,而连续流动技术显著优于批量方法,E因子范围为2到20,因此平均减少了87%。这种改善可归因于连续流动技术的内在特性,包括整体更高的产率、更低的废物产生和溶剂使用的最小化。
案例研究
1、案例研究一:青蒿琥酯(Artesunate):闭环生产实现零溶剂排放
青蒿琥酯传统工艺依赖高毒性溶剂(如甲苯)和低温反应,环境风险高。连续流工艺闭环生产实现零溶剂排放,这不仅减少了环境污染和操作风险,还通过高效的溶剂回收和反应控制,提高了生产效率和资源利用率,从而显著降低生产成本。
技术突破:溶剂100%循环:集成在线蒸馏模块,甲苯回收率从40%提升至98%,年减少采购成本80万美元。反应时间缩短75%:停留时间从8小时压缩至2小时,产能提升至200公斤/天。E因子从105→3:THF用量从17.1g/g降至0.1g/g,危废处理成本降低90%。碳排放降低:碳排放从0.38kgCO₂/g降至0.05kgCO₂/g,每吨减少330吨碳排放。节省水资源:水资源消耗从0.0072m³/g降至0.0039m³/g,年节水超1万吨。
2、案例研究二:Amitriptyline:精准控温消除副反应,纯度提升至99%合成涉及高风险中间体,传统工艺副反应多、安全性差。连续流工艺的开发精准控温消除副反应,纯度提升至99%。连续流工艺优势:杂质率降低90%:精准控温(±0.5℃)将副产物从12%降至1.2%(案例来源:Kupraczetal.)。THF用量减少80%:静态混合器强化传质,THF用量从23.3g/g降至4.7g/g。产能提升3倍:年产量从50吨增至150吨,满足全球需求。碳排放降低95%:碳足迹从0.43kgCO₂/g降至0.02kgCO₂/g,降幅95%。单位能耗降低:能耗从102kWh/kg降至22kWh/kg,年节省电费25万美元)。
3、案例研究三:布洛芬(Ibuprofen):能耗降低97%,成本与效率双赢布洛芬作为全球用量最大的非甾体抗炎药,传统批处理工艺存在反应时间长、溶剂消耗大、能耗高等问题。通过优化为连续流工艺,能耗降低97%,实现了成本与效率的双赢,不仅显著减少了环境影响,还提升了生产经济性。
技术突破:溶剂用量减少84%:连续流闭环溶剂回收系统使甲醇用量从48.2g/g(批处理)降至3.5g/g(连续流工艺),年节约成本超50万美元。这种减少进一步降低了对土地系统的影响和环境足迹。能耗断崖式下降:连续流技术通过精准控温(±0.5℃)和高效传质,将单位能耗从批处理的9.51W·h/g降至连续流工艺0.82W·h/g,降幅达97%。降低97%碳排放:从批处理0.41kgCO₂/g降至连续流0.01kgCO₂/g,每吨布洛芬减少400吨碳排放,布洛芬连续流工艺的碳排放降低了97%。低投资成本:布洛芬连续流工艺的资本成本较低,批量配置的估算成本在300万美元到700万美元之间,而连续流动技术的成本范围在200万美元到400万美元之间。高盈利能力:15年净现值(NPV)分析显示,连续流工艺可提前3年回本,长期利润增长斜率高60%。
未来展望
连续流技术不仅是工艺升级,更是制药业绿色转型的核心引擎。随着智能化、模块化技术的深度融合,其将在降本增效、资源循环、全球合规三大维度持续释放价值,推动行业向“零废弃、零碳排”的可持续未来加速迈进。